reman group engines
Manufacturing Process
Phases of the manufacturing process
At Reman Group Engines, we follow a rigorous and meticulous remanufacturing process to restore used engine components to like-new conditions, meeting OEM specifications and ensuring reliable performance. Unlike rebuilt or repaired engines, our remanufactured engines undergo a complete restoration, including disassembly, machining, testing, and final assembly.
Receiving & Disassembly
• Used engines and components, known as “shells,” are received, classified, and stored.
• The disassembly line removes key components (blocks, heads, crankshafts, rods).
• Each part is inspected and sorted to determine if it can be reused.
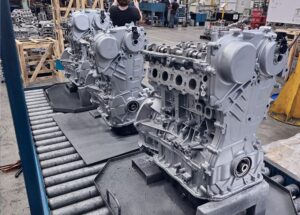
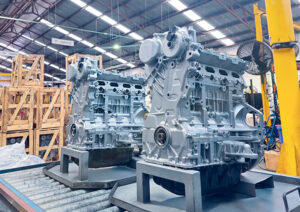
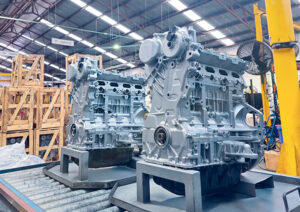
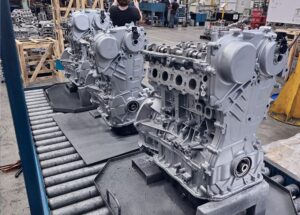
Diagnosis & Preparation
• Engine blocks are sent to the Cylinder Grinding Department.
• Precision honing and resizing restore cylinders to exact specifications.
• If a cylinder is too damaged, sleeves or inserts are installed to maintain structural integrity.
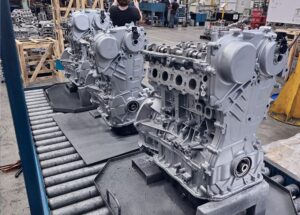
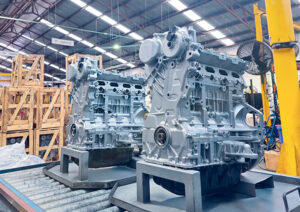
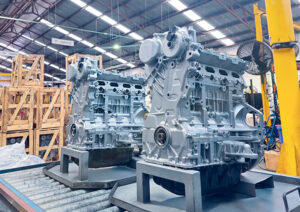
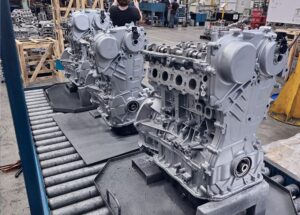
Block Machining
- Multi-step cylinder honing ensures precision
- Processes include:
– Surface Grinding for proper gasket sealing.
– Bed Honing to achieve exact dimensions.
– Cleaning & Rinsing to remove contamination.
– High-Pressure Washing to eliminate impurities.
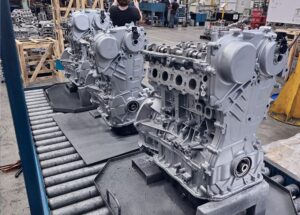
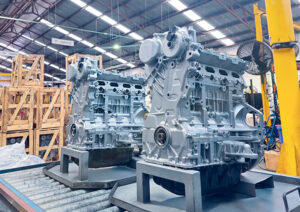
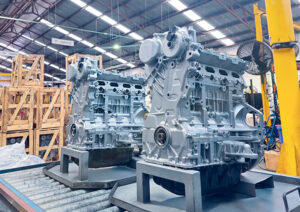
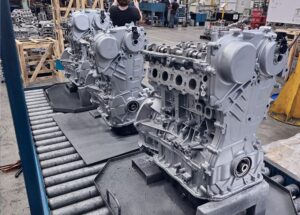
Connecting Rods Processing
- Rods undergo inspection, classification, and precision grinding.
- Alignment verification ensures rods meet manufacturer tolerances.
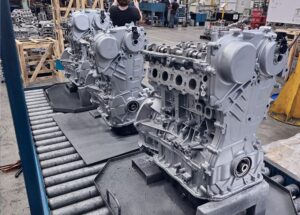
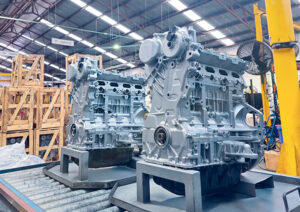
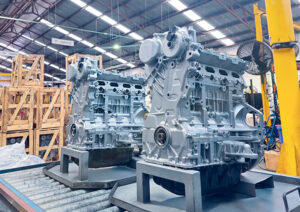
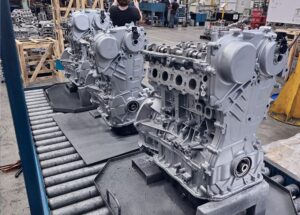
Valve Processing
- Valves are sorted, machined, and polished to achieve original-equipment texture.
- Stem, face, and tip grinding ensure a perfect seal and functionality.
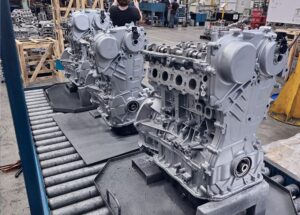
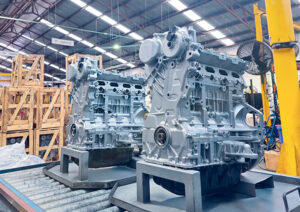
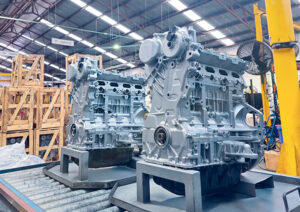
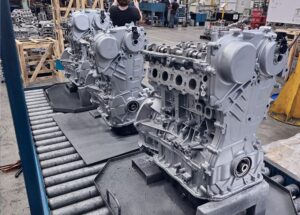
Small Parts Inspection
- Rocker arms, springs, screws, and flanges are cleaned, classified, and tested.
- Only approved parts move forward for assembly.
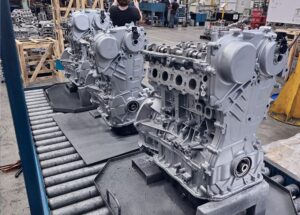
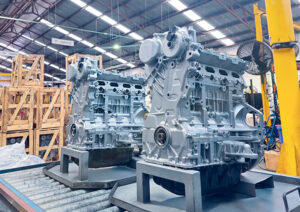
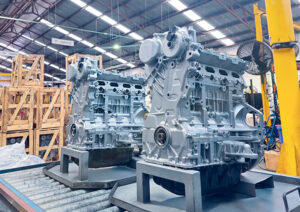
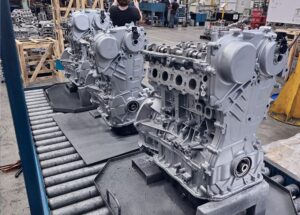
Deep Cleaning & Preparation
- Blocks, heads, and crankshafts go through:
– Oven baking & shot peening to remove residues.
– Biodegradable caustic cleaning for valves and rods.
– Vibrating machines for precision polishing.
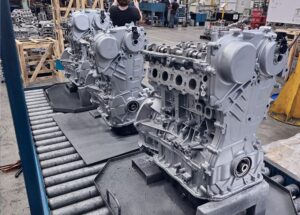
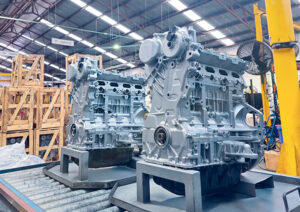
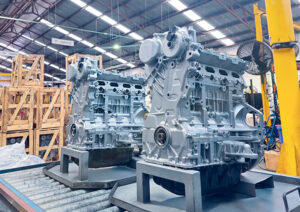
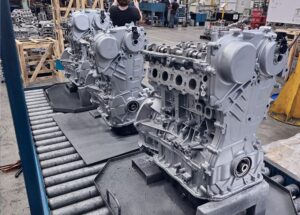
Crankshaft Diagnostics & Preparation
- Crankshafts are measured, inspected, and repaired.
- Thread repair and defect correction restore integrity before machining.
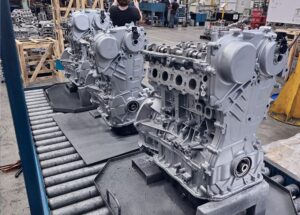
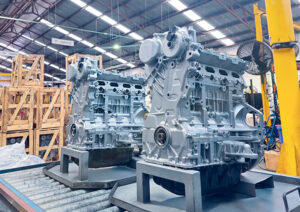
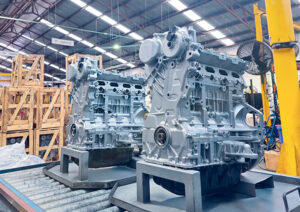
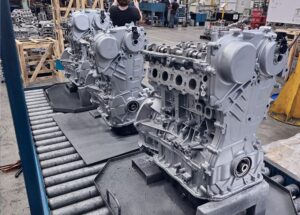
Head Diagnostics & Preparation
- Magnetic testing (Magnuflux) detects hidden cracks.
- Welding & repairs ensure all heads meet OEM specifications.
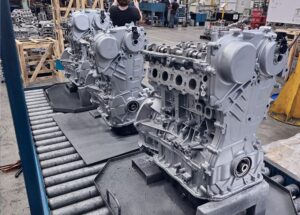
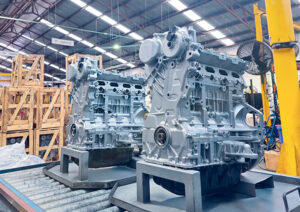
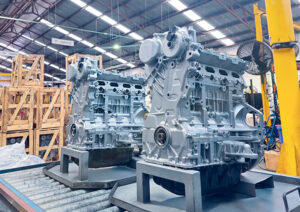
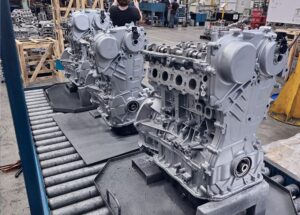
Machining of Heads
- Bronze guide installation, seat rectification, and surface finishing guarantee longevity and efficiency
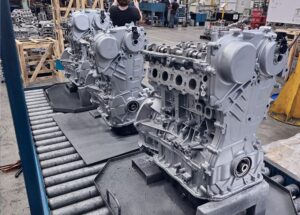
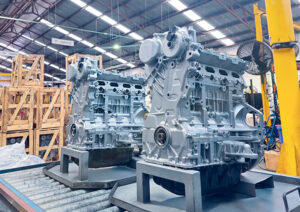
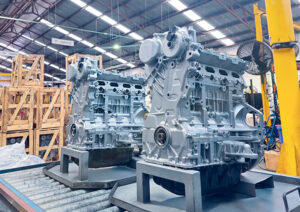
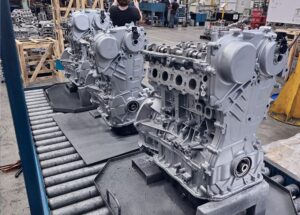
Machining of Crankshafts
- Journals are ground & polished for optimal lubrication and performance.
- Chamfering & micropolishing ensure precise tolerances.
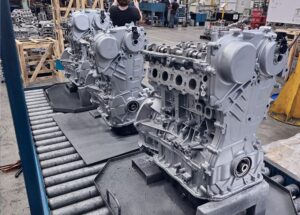
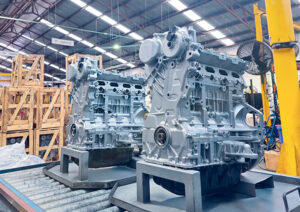
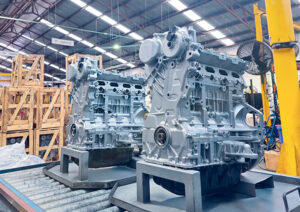
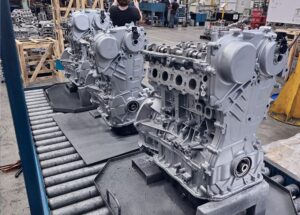
Assembly
- The assembly line integrates all components into a fully functional engine, ensuring perfect alignment, lubrication, and fit.
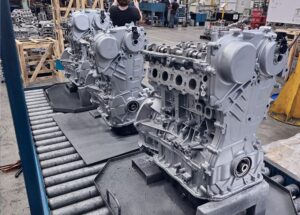
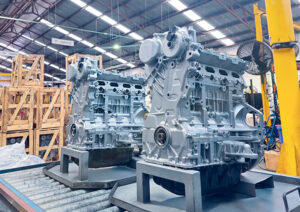
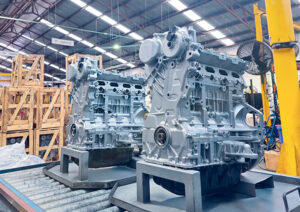
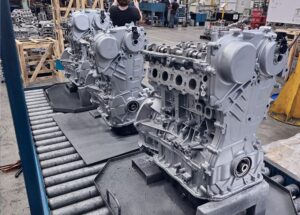
Testing, Inspection & Shipping
- Engines undergo leak tests, pressure checks, and computerized simulations.
- Painting, packaging, and secure shipping guarantee a ready-to-install product.
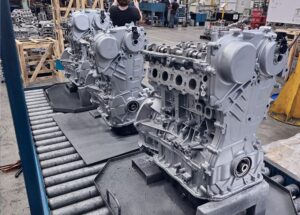
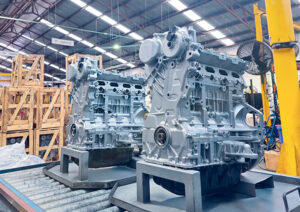
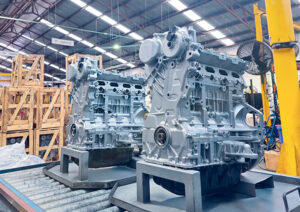
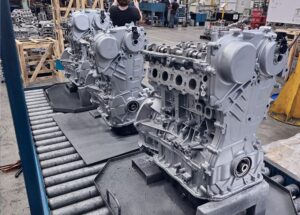